Why a Reliable Chemical Defoamer Is Crucial for Maintaining Manufacturing Productivity
Why a Reliable Chemical Defoamer Is Crucial for Maintaining Manufacturing Productivity
Blog Article
Comprehending Just How a Chemical Defoamer Works to Enhance Industrial Processes
Chemical defoamers play a crucial role in optimizing industrial procedures by properly mitigating foam-related challenges. Their capability to reduced surface stress and interfere with bubble development translates into smoother operations and enhanced effectiveness. The systems behind their action and the variety of readily available formulas require a closer evaluation. Understanding these aspects could reveal significant insights into not only enhancing production however likewise accomplishing expense savings across multiple sectors. What remains to be explored is just how these defoamers can be tailored to meet specific functional needs.
What Is a Chemical Defoamer?
A chemical defoamer is a substance specifically created to eliminate the development or decrease of foam in numerous commercial processes. Foaming can conflict with manufacturing efficiency, affecting the top quality and performance of items in markets such as food and drink, pharmaceuticals, and wastewater treatment. Defoamers are crucial in these applications, as too much foam can cause operational obstacles, such as overflow, decreased blending effectiveness, and hindered warmth transfer.
The choice of a proper defoamer is important, as various solutions may be customized for specific processes or kinds of foam. Elements such as compatibility with various other ingredients, temperature security, and the desired application play a significant function in the performance of a defoamer.
Mechanisms of Defoaming Action
The devices of defoaming action entail complex interactions in between the foam and the defoamer framework. At the core of this procedure is the reduction of surface area stress at the user interface of the liquid and gas phases. When a defoamer is presented to a frothing system, it migrates quickly to the surface of the foam bubbles, displacing the stabilizing representatives that add to foam stability. This displacement deteriorates the foam framework, leading to bubble coalescence.
As smaller sized bubbles combine right into bigger ones, the total security of the foam diminishes. Additionally, certain defoamers may include hydrophobic elements that improve their capability to destabilize the foam by creating a barrier that inhibits bubble formation. This twin activity-- surface area stress decrease and destabilization-- permits a much more effective malfunction of foam.
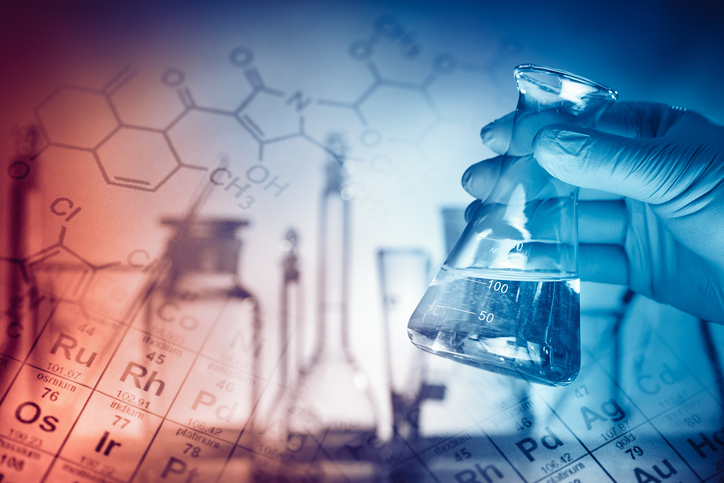
Additionally, the viscosity and spreading characteristics of the defoamer play crucial duties in its performance. A well-formulated defoamer will certainly make certain quick movement and optimal performance, decreasing foam development during industrial procedures. By recognizing these mechanisms, sectors can better select and use chemical defoamers to enhance operational efficiency and item high quality.
Kinds Of Chemical Defoamers
Chemical defoamers can be classified right into a number of kinds, each customized to certain applications and foam challenges. The primary classifications include silicone-based, non-silicone-based, and powder defoamers.
Silicone-based defoamers are very efficient due to their capacity to spread out rapidly throughout fluid surface areas. They give outstanding foam suppression and security, making them suitable for numerous industrial applications, consisting of finishes and adhesives. Non-silicone-based defoamers, on the other hand, commonly count on natural substances like fats or esters. These are particularly preferred in food and beverage sectors because of their reduced toxicity and governing compliance.
Powder defoamers consist of solid fragments that can be contributed to completely dry processes or solutions. They are frequently made use of in processes where liquid defoamers might not work, supplying an unique option for details applications, such as in the production of specific kinds of plastics or powders.
In addition, each kind of defoamer can be personalized with numerous additives to pop over to this web-site boost efficiency, such as emulsifiers or surfactants, permitting versatility in dealing with various frothing circumstances throughout numerous markets.
Applications in Industrial Processes

In the food and drink market, defoamers are critical during the production of juices, beers, and milk items, where extreme foam can hinder mixing and purification processes. By decreasing foam development, defoamers assist keep constant product top quality and optimize handling times.
In pharmaceuticals, the visibility of foam during the blending and formula of medicines can influence dosage precision and product security. Defoamers ensure smooth procedures, thereby promoting the manufacturing of top quality drugs.
Wastewater treatment facilities also count on defoamers to control lathering in oygenation tanks, which can or else reduce treatment performance and complicate sludge handling. By properly managing foam, these chemicals improve the total performance of treatment procedures and add to regulative conformity.

Benefits of Using Defoamers
While foam can present substantial obstacles throughout different markets, making use of defoamers offers numerous benefits that boost operational efficiency and item honesty. Defoamers successfully minimize or get rid of foam development, causing smoother production processes and boosted product high quality. This decrease in foam lessens interruptions during production, enabling constant operation and raised throughput.
Additionally, the application of defoamers can result in cost financial savings by reducing the need for excess basic materials and energy consumption connected with foam administration. By optimizing the manufacturing process, manufacturers can accomplish higher returns and lower waste, inevitably enhancing profitability.
In addition, defoamers add to far better devices efficiency. Foam accumulation can lead to blocking, overflow, and equipment wear, causing costly downtime and upkeep. By preventing these problems, defoamers extend the life expectancy of machinery and minimize functional expenses.
Verdict
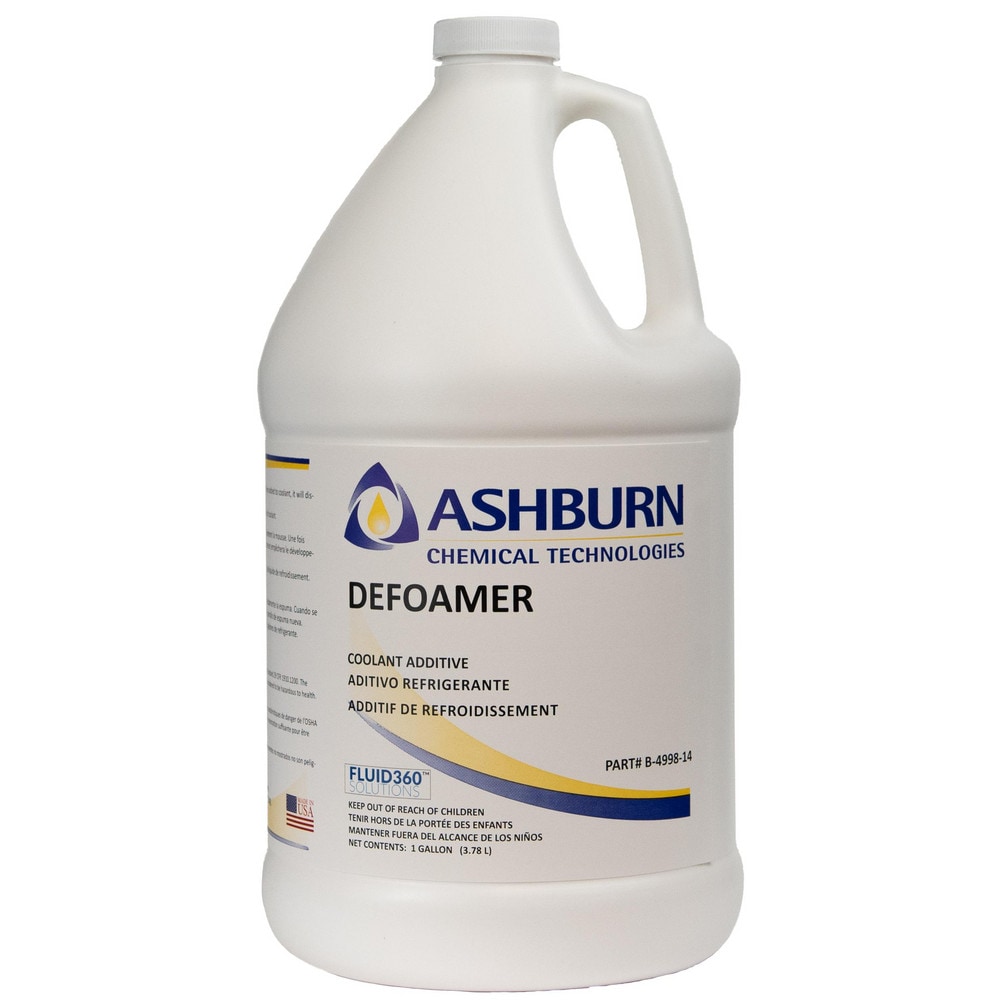
A chemical defoamer is a material particularly formulated to lower or get rid of the development of foam in numerous industrial procedures. When a defoamer is introduced to a foaming system, it moves rapidly to the surface area of the foam bubbles, displacing the supporting agents that add to foam stability. A well-formulated defoamer will certainly guarantee quick movement and optimum efficiency, decreasing foam development throughout commercial procedures. Defoamers successfully lower or remove foam formation, leading to smoother manufacturing processes and enhanced product high quality.In conclusion, chemical defoamers play an essential role in boosting industrial procedures by effectively minimizing foam Source formation.
Report this page